Quadwalker
Motorized Walking Stick Designed for Enhanced Patient Safety
summary_
Quadwalker is a motorized device designed to be mounted on any existing quad cane. It was designed to enhance the safety of existing quad canes by removing the need for users to lift the cane high off the ground throughout his/her walking gait.
Year 2014
Team Stevanus Satria, Zhang Zheyang (Jack), Sun Xinning, Liu Wendong
My Role Designer, Electronics Engineer
Hardware MakerBot Replicator 2
background_
The objective of one of our sophomore year projects was to design new or improve existing assistive/rehabilitative devices. Our group decided to focus on the elderly and patients undergoing mobility rehabilitation, such as those who suffered severe leg injuries. One of the most common devices used by these individuals was a walking stick or walking frame.
These walking sticks or frames come in many different flavors, and they are generally quite affordable. However, we were concerned with the way these sticks or frames have to be lifted off the ground cyclically throughout the user’s walking gait, as shown by the animated GIF below:
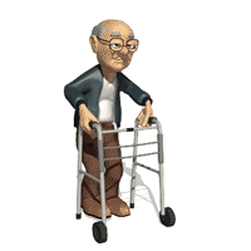
In the case of a walking frame, the user remains in a relatively upright position due to the way he/she utilizes both arms evenly when lifting up and pushing down the frame. However, in the case of a walking stick, the user generally leans to one side when he/she pushes down on the stick. If the user does not stabilize himself/herself properly before lifting the stick forward, he/she might lose balance, and the result might be catastrophic.
Hence, the group aimed to reduce this risk by reducing both the time the walking stick is airborne and the distance it lifted off from the ground throughout the user’s walking gait.
To reduce the airborne time of a walking stick and its distance from the ground throughout a user’s walking gait
THE GOAL
research_
We decided not to design our own version of a walking stick. The reason being that the walking stick has been around for a long time and a single purchase can generally last a lifetime. As such, we aimed at augmenting the existing designs’ functionality instead.
For our design project, we decided to focus on the quad cane. A quad cane is a four-legged version of a traditional walking stick. Similar to the latter, a quad cane is meant to be used one-handed, on the side that requires more support. The advantage of a quad cane over a traditional walking stick is its increased stability due to its overall wider base.
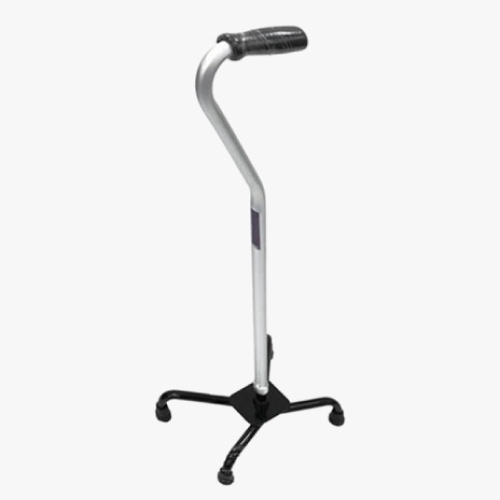
Going back to analyzing a user’s walking gait, we realized that in general, the further he/she wants to move the stick forward, the higher he/she lifts the walking stick. At the same time, the higher the walking stick is lifted from the ground, the longer it takes for the user to bring it down should he/she suddenly needs support. This provided us with the idea of eliminating the correlation between forwarding distance and airborne distance. We postulated that having a perpetually short airborne distance regardless of the forwarding distance desired meant immediate and sudden access to support is always viable for the user.
overall solution design_
We took a closer look at images of the quad cane as we waited for our procured item to arrive, and noticed an available within the four legs of the base. We realized that we could design a motorized device to be mounted within that space, which would allow the cane to be moved forward as far as desired without having to lift it up higher. However, we needed to figure out how to start and stop the device’s motion on-demand.
After brainstorming for a few more days, we finally came up with a spring-loaded mechanism to solve this problem. When the user pushed down on the cane, a force would be exerted on a switch-like component, which would stop power from being transmitted to the motors. At the same time, the grips mounted on the four legs of the cane would press firmly against the ground, thus providing stable support to the user. When the user lifted the cane up, the force would be relieved as the legs were lifted off the ground, and power would be transmitted to the motor, which subsequently moved the cane forward.
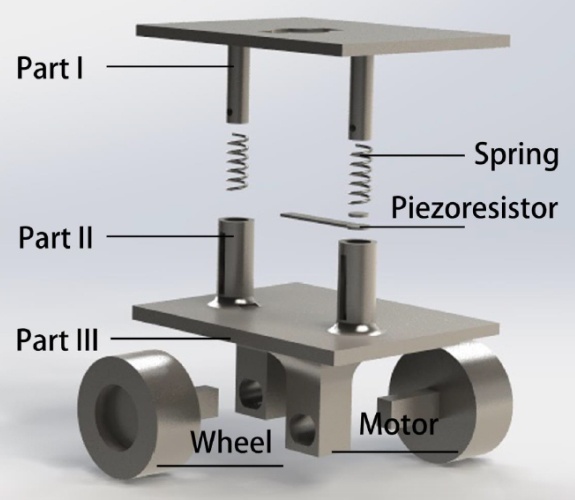
Having arrived at this idea, we went ahead to split the tasks at hand amongst ourselves, and I was entrusted with designing the circuitry for the motors and the force-sensitive resistor.
electronics_
The aim of the circuit was to (a) activate the driving motors of the walking stick when the pressure was released from the walking stick and (b) stop the motors when pressure was applied on the walking stick when the user attempted to walk. This could be achieved by adjusting the potential difference across both motors. Considering the final design’s limited area of 45 mm x 80 mm x 30mm during compression, the circuit should be small and compact. To reduce the space occupied by the AA-size alkaline batteries, they were soldered and packed closely with insulated rubber tape instead of mounted in a casing.
The simplest way to adjust the potential difference across the motors was to use a potential divider circuit, using either (a) a push-to-break switch or (b) a force-sensitive resistor (FSR). On one hand, the push-to-break switch was bulkier and only provided two modes of operation: on and off. On the other hand, despite the FSR being thin, easy to mount, and providing a gradual change of its resistance with respect to pressure, it was difficult to control the circuit since the motors were parallel to the FSR which resulted in a significantly smaller and possibly more unstable resistance compared to R1.
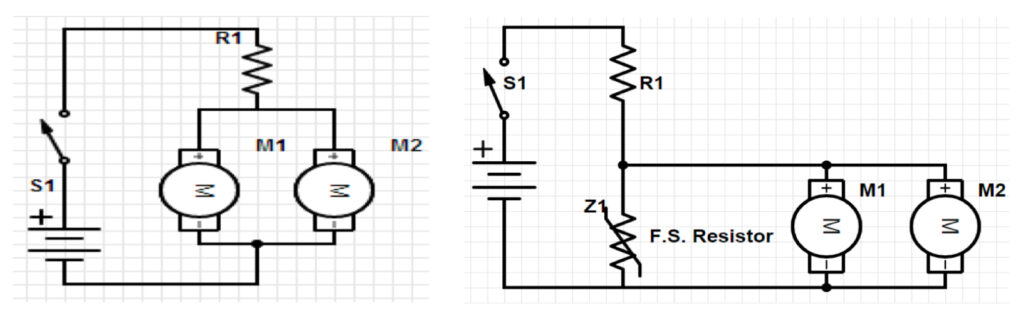
To reduce the interactions between the source and the motors, a separation between the sensing circuit and control circuit was required. Two designs were taken into consideration during ideation: (a) comparator circuit with MOSFET as a switch and (b) potential divider circuit with MOSFET as an amplifier.
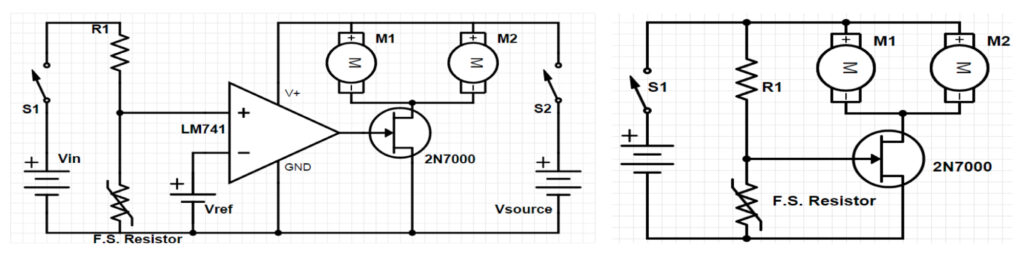
Having multiple sources was not ideal as it would consume more space and increase the weight of our product. The use of more sophisticated components such as the operational amplifier, although feasible, was not preferred as it required at least two sources with the assumption that the input source and the operating source were integrated. The other design is to combine the potential divider circuit with a MOSFET as an amplifier, which eventually became our preferred design as it satisfied the space limitation of the system.
assembly_
We printed the device’s housing in PLA using the MakerBot Replicator 2. The circuitry, on the other hand, was wired on a prototype universal PCB cut out to the right dimension. During assembly, we accidentally broke the two force-sensitive resistors we had procured! Luckily, a local supplier we got in touch with had the part in stock and were kind enough to deal with us even though it was close to midnight. Thanks to that, we managed to assemble everything shortly after midnight. A quick test run followed and to our delight, the prototype worked flawlessly!
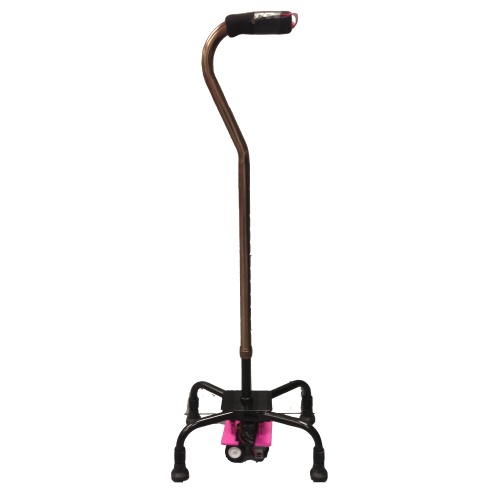
evaluation_
After assembling the device onto the quad cane we procured and ironing out small kinks, we managed to get reliable results with it! The device ended up weighing only 200g, which was significantly less than the quad cane’s 1.3kg. It could be easily mounted on any quad canes in the market, a feature that was born from the team’s realization of the longevity of a single quad cane purchase. However, we also acknowledged that there was room for improvements, such as the redundancy of one of our springs, the possible redundancy of our second motor, and the possibility of better wiring for the main switch which we routed up to the handle. Nonetheless, given the budget and timeline constraints, all of us were extremely pleased with what we managed to achieve!
And so were our professors 🙂